発刊の動機と目指したいもの
必要な部分には必要な信頼性を適正コストで
と書きましたが、必要でない部分にオーバースペックは不要である。ともいえます。現在、業務実績に示しましたが色々な立場で仕事をしています。
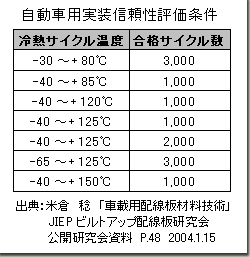
例えば、右表の信頼性評価条件がありますが、現実的にどの試験条件が適切で、
かつ、表示されている合格サイクル数がフィールドで何年に相当するかの加速係数をあまり目にしたことがありません。
著者は例えば、-65〜+125℃ 3000サイクルは相当オーバースペックであると考えています。基板メーカ様、その下請け様の立場では、セットメーカ様の仕様なのでスペック変更はどうにもならず、逆にセットメーカ様の立場で仕事をしている場合、この基準の根拠は?と伺ってみると曖昧な場合があります。
結局、「必要な信頼性を適正コストで」の答えは藪の中です。著者紹介で示しましたが、著者は高信頼性を要求される産業機器に、上記の表よりかなり緩い基準を適用して自身の職場で作った基板あるいは外部基板メーカから調達した基板を色々な製品へ適用し、その製品の寿命期間を終えるまでの間在籍し監視していた経験があります。
20数年間事故を起こさなかった経験からオーバースペックの部分について、業界関係者の皆様に基準・評価条件の適正化を呼びかけたいと考えています。同時にプリント板製造についてセットメーカに所属していた経験からの品質管理のポイントをお話したいと考えます。
車載基板ビジネスと信頼性
車載関連ではITS(Intelligent Transport Systems: 高度道路交通システム)市場に「2015年までの市場規模は約60兆円」(総務省電気通信技術審議会、99年予測)とありますが、少し前には「税金を使ってやることが問題だ」「自動車・電機メーカは儲からないITSに少しずつ距離を置き始めた」との慎重論の報道もありました。
しかし、平成18年3月9日開催の国土交通省道路局主催「第5回スマートウェイ推進会議作業部会」注)ではスマートウェイとして、全国にDSRC(Dedicated Short Range Communication: 狭域無線通信)を普及させようとソフト・ハードウェアの仕様が固まり、いよいよITSの本格稼動の時期が到来したと思えます。スマートウェイで必要とするハードウェアは@ITS車載機 ADSRC側路無線装置 です。いずれも、プリント板への大きな市場になると思われます。
注)
クリックして表示されるホームページで右側の「スマートウェイ」リンクボタンをクリック。
「スマートウェイ推進会議関連の新着情報」で06/04/05のリンクをクリック。
色々な資料のダウンロードが可能。
ここで著者が心配するのは、ITSに限ったことではありませんが「これらハードに用いるプリント板の要求信頼度を誰が決めるか」です。特に、ADSRC側路無線装置及びその関連アプリケーションについては多数の新規メーカの参入が可能のはずです。仮に、著名なセットメーカの一握りの技術者がオーバースペックを適用すると、その会社のネームブランドで一斉にそれが業界標準のようになり、ハイスペックであるが故に新規メーカの参入が困難になることを懸念します。
アプリケーションの用途に応じて適切な信頼性とコストでもの作りをするべきだと考えています。
信頼性とモデリング能力
『信頼性向上のためエンジニアに求められるものは「モデリング」能力』
元某大手電機メーカ、品質保証ご担当のベテラン部長さんの言葉で著者が感銘を受けたものです。
一つのデータから事実を予測できる「モデリング能力者」が不足している。これは、製造メーカにおける信頼性向上や新製品開発だけでなく教育現場でも不足している。「製品品質はエンジニアの品質で決まる」。つまり、モデリング能力を上げるには、サンプル数は少ないけれども、一つのデータ(点)を深く掘り下げ、その都度考察を加えていくことが、面の事実を予測するための正確なパラメータ(要因)を摘出できることになる。とのことです。
なぜ、セットメーカの技術者の方はオーバースペックと思える基準を提示されるのか。それは、ご本人の皆様方も試験条件とフィールドとの現実的な相関データを持っていないから沢山の保険をかけざるを得ないのだと推定します。そこで、この資料はサンプル数少ないけれども先ず実物を見て少しでも実物と机上データの乖離を埋めたいと考えています。実物をよく観察し、0(ゼロ)と1(イチ)見たか、見ないかの差は大きいものがあると考えます。そして、読者の皆様と意見を共有し、より適切な信頼性とコストでのもの作りに繋がれば幸いと考えます。

右の写真はジョークですが、実際の車に試験片と環境を記録するデータロガーを取り付け、10年程度データを取ったらどうなるでしょうか。適宜、マイクロセクションをしてスルーホールの劣化状態を観察します。個人ではとても無理です。
しかし、自動車メーカとタクシー会社が提携してデータを取ることは不可能ではないでしょう。同時に作った基板を加速試験にかければ、本当の加速率と相関関係が分かります。
目指したいもの
日本のプリント板技術はこの先どこに行くのでしょうか。ビルトアップ基板、全層一括積層基板あるいは様々なサブストレートが登場してからプリント板の技術は飛躍的に進化しました。しかし、極めて泥臭いベーシックな部分がなおざりにされているのではないかと著者は感じています。
時々、中国の大手基板メーカ様にお邪魔しますが、設備能力、技能、労働コストにおいて残念ながら、日本国内の大半の基板メーカ様には厳しいものがあると思います。もし、優秀な商社と物流、数人の技術者がいればどうなってしまうのだろうかと。
すでに21世紀に入っています。日本のプリント板関係者の皆様には更なる困難なもの作りができるようにと、今こそもう一度ベーシックな部分に戻り、「必要な信頼性を適正コストで」を実現できるように基礎的な部分をブラッシュアップしても良いのではないかと考えます。
プリント板の黎明期から携わり、ここ数年の間にリタイヤされた先輩諸兄を探し、信頼性について「今だから語れる○○○」など生き証人としての貴重な宝のお話を取材してこのWebに掲載し次の世代に引き継いでいきたいと考えます。定量データは得られないかも知れませんが、皆様のモデリング能力があればきっとプリント板の適正コストでの信頼度設定へお役に立てると考えます。
もちろん、現役の方、匿名でも結構です。色々なご意見・情報をいただけることを歓迎いたします。そして、欲を言えば将来このWebはノウハウを扱っているプリント板のポータルサイトに育てられればと考えています。困った時、このWebに来れば何か手がかりが探せるようにと.....。